EL VIDRIO
El vidrio es un material inorgánico duro, frágil, transparente y amorfo que se encuentra en la naturaleza, aunque también puede ser producido por el ser humano. Es inodoro, no altera el sabor, es reutilizable y fácilmente reciclable. No tiene una estructura cristalina, las partículas que lo forman están ordenadas al azar. Su estado es un líquido muy viscoso llamado vítreo.
Se obtiene a unos 1500 °C a partir de arena de sílice, carbonato de sodio y caliza.
Todas estas propiedades han llevado a algunos investigadores a definir el estado vítreo no como un estado de la materia distinto, sino simplemente como el de un líquido con una viscosidad tan alta que le confiere aspecto de sólido sin serlo. Esta hipótesis implica la consideración del estado vítreo como un estado metaestable al que una energía de activación suficiente de sus partículas debería conducir a su estado de equilibrio, es decir, el de sólido cristalino. Los cuerpos en estado vítreo no presentan una ordenación interna determinada.
Debido a los distintos tipos de vidrios que pueden ser fabricados, las densidades varían de acuerdo a la sustancia con la que sean complementados; normalmente un vidrio puede tener densidades relativas.
Para la fabricación del vidrio se funden y se mezclan los siguientes materiales:
- Sílice: es el principal componente del vidrio (más de un 60%), y se obtiene a partir de la arena.
- Carbonato o sulfato de sodio o potasio: sirve para que el sílice funda a menor temperatura.
- Piedra caliza: su función es estabilizar la mezcla y darle durabilidad.
Añadiendo otros ingredientes se puede dar al vidrio determinadas propiedades físicas y características según las aplicaciones técnicas a las que se quiera aplicar.
El vidrio es un producto de la combustión y fusión de la arena. El resultado es una estructura molecular muy poco compacta y organizada. El grado de transparencia de un material viene determinado por la cantidad de luz que éste deja pasar en comparación con el total que llega a la superficie.
El vidrio es frágil porque una red de fisuras a nivel imperceptible que afectan a la superficie del vidrio y provocan unas tensiones localizadas que disminuyen la resistencia mecánica del vidrio. Son las fisuras de Griffith y cada una de ellas puede ser el origen de una ruptura general. Encontramos una diferencia de fragilidad entre el vidrio y el cristal considerable. Un vidrio es un silicato que en estado líquido tiene las moléculas formando anillos desordenados y incompletos con átomos de sodio incluidos. Enfriando este líquido a gran velocidad, para que al pasar de líquido a sólido no cristalice, obtendremos un sólido no cristalizado al que llamaremos vidrio. Si el vidrio cristaliza, es decir que se enfría lentamente, las moléculas se ordenan geométricamente obteniendo un cuerpo más opaco y mucho más frágil.
Tiene una dureza media, es decir, su resistencia a ser rayado es de grado 5/6 sobre 10(escala de Mohs)
Sólo se comportará plásticamente a altas temperaturas. A partir de 600 º C se deforma plásticamente y en 1000 º C se funde.
Resistencia: Aunque los cristales se pueden formar con materiales diferentes, la mayoría de propiedades son consecuencia directa del estado físico en que se encuentra el vidrio. La composición básica del vidrio es Silicio-Oxígeno.
Tracción: Teóricamente: soporta 70 000Kg/cm2 , 5 veces más que el acero. Prácticamente: soporta 400/1000Kg/cm2. Valor muy inferior debido a las fisuras de Griffith. Varía en función del tipo de vidrio y tratamientos a los que haya sido sometido.
Comprensión: soporta 10.000Kg/cm2. Cualquier fuerza aplicada sobre el cristal se concentrará sobre cualquier irregularidad en su superficie y debido a que es un material homogéneo porque viene del líquido, las grietas se propagan muy rápidamente.
VIDRIO TEMPLADO
- Es un cristal que ha sido sometido a un tratamiento térmico de cambio de temperatura súbita que modifica sus propiedades físicas.
- La cara superficial se enfría rápidamente y el cuerpo central tarda más, lográndose esfuerzos de compresión en las caras externas (100 N /mm2) y de tracción en el interior.
- Este tratamiento aumenta su resistencia al choque mecánico (x4) y térmico (x6), así como a flexión, sin afectar demasiado sus cualidades ópticas.
- Se caracteriza por su seguridad ya que, en caso de golpe, se fragmentará en trocitos pequeños evitando heridas y otros daños perjudiciales. Otra característica es la resistencia a la flexión. La resistencia al choque térmico es otro aspecto importante de este producto (rotura por diferencia de temperatura en un mismo cristal.
VIDRIO LAMINADO
- Es un conjunto formado por dos o más planchas de vidrio, unidas entre sí, entre las cuales hay una película intermedia de láminas de PVB (butiral de polivinilo) elástico. Se unen en un proceso de autoclave con calor y presión.
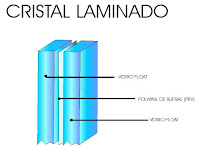
- El vidrio laminado se caracteriza por su seguridad, presenta una buena resistencia al impacto. Cuando recibe un golpe, la rotura se localiza en el punto de impacto y mantiene la transparencia. La lámina de PVB asegura que las piezas de vidrio se mantengan adheridas. Reduce el riesgo de cortes por fragmentos de vidrio o caídas a través del cristal laminado. El PBV es elástico, con fuerte adherencia y puede ser transparente, opaco o de cualquier color.
- La acústica es otra propiedad importante. Estos cristales ofrecen una atenuación acústica muy superior a la del vidrio monolítico del mismo grosor. Los valores de aislamiento acústico de un PVB acústico son superiores a los cristales laminados con un PVB clásico.
El templado
- Es un tratamiento térmico del vidrio:
1 - Se calienta el vidrio hasta que sea algo plástico, a unos 600 º C.
2 - Se enfrían rápidamente las caras exteriores, de manera que se solidifican nuevamente.
3 - La banda central es aún plástica y se va enfriando, por tanto, se contrae. Se contrae pero está unida a las caras exteriores ya sólidas, que se ven comprimidas por el arrastre que la banda central provoca.
- El resultado es un cristal "pretensado", Con las caras exteriores sometidas a una compresión interna y la banda interior traccionada.
VIDRIO ARMADO
• Es aquel vidrio que se obtiene por proceso de colado.
• En el vidrio armado, se le deja embebido en su interior una malla metálica en forma de retícula, de modo que en su rotura los trozos quedan unidos al metal evitando su caída y posibles lesiones. Aún así, no es muy adecuado si se expone a temperaturas extremas. Estos cambios de temperatura dan lugar a la dilatación de ambos materiales, que pueden provocar la rotura del vidrio.
VIDRIO RESISTENTE A ALTAS TEMPERATURAS
- Su objetivo es aislar el calor. Tener suficiente resistencia para aguantarlo sin ningún tipo de modificación (rompiéndose o fundiéndose) y eliminar o limitar la probabilidad de que se transmita un incendio.
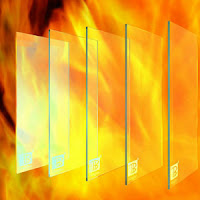
- Se obtiene añadiendo una sal (borosilicato de sodio) a la masa del vidrio en fabricación, este componente reduce notablemente el coeficiente de dilatación del vidrio (1/3 del vidrio común).
- Hay una serie de características básicas que deben tener los vidrio usados con el objetivo de tener seguridad ante incendios:
1.- Estabilidad o resistencia mecánica a los cambios térmicos (Dilatación controlada): Se consigue añadiendo aditivos a la masa del vidrio (borosilicato de sodio).
2.- Estancamiento de las llamas, humos y gases calientes y/o inflamables.
3. – Aislamiento térmico por reducción de la radiación (Manteniendo durante un cierto tiempo el vidrio con una temperatura no elevada).
Vidrios en el mercado
Cristales parallamas : Vidrio con borosilicato de sodio que incorpora además una lámina armada. Siempre transparente. No evita la transmisión de temperatura.
Cristales cortafuegos: Vidrio con láminas intumescentes que reaccionan a temperaturas superiores a 120 grados volviéndose rígidas y opacas. Evita transmisión de temperatura.
La conductividad térmica es una propiedad física de los materiales que valora la capacidad de transmitir el calor. Su inversa es la resistencia térmica que es la capacidad de los materiales para oponerse al paso del calor. Cuando la radiación solar incide sobre un cristal, una parte es reflejada hacia el exterior, otra pasa directamente hacia el interior y la restante es absorbida por la masa del vidrio. El vidrio permite la transmisión de la radiación solar entre las longitudes de onda de 315 y 2.500 nm, es decir, desde el rayo ultravioleta hasta casi todo el infrarrojo. El ultravioleta por debajo de 315 nm y el infrarrojo de onda larga por encima de 2.500 nm se absorben por completo. Esta impermeabilidad a las radiaciones de onda larga explica el efecto invernadero y varios usos concretos del vidrio.
- Modos que tiene el vidrio de transmitir el calor:
- Por la condición de sólido transmite el calor por conducción.
- Por su característica transparente transmite el calor por radiación.
- Por conducción, en los cristales con cámara, ésta no es demasiado gruesa para dificultar l transmisión de calor: siempre se produce desde un espacio o cuerpos más calientes a unos menos calientes.
-Aislamiento térmico: al igual que otros materiales (un techo) depende del coeficiente de conductividad térmica de los materiales, componentes y la forma en que es utilizada.
VIDRIO CON CÁMARA DE AIRE
- Es un cristal formado por al menos dos piezas de vidrio separadas por una cámara de aire deshidratado, dispuestas paralelamente y formando una única unidad de vidrio.
- Su característica diferenciadora es un importante incremento del grado de aislamiento térmico.
- La cámara de aire también puede estar llena de algún gas noble (argón o kriptón) los cuales mejoran las propiedades de aislamiento térmico.
VIDRIO ANTIRREFLECTANTE
- Posee un tratamiento en las dos caras a base de aplicación de capas metálicas logrando así la disminución de la reflexión de la luz sin distorsionar los colores (pasa del 8% al 1%).
- Este producto es muy útil porque se le puede aplicar el proceso del templado y laminado, consiguiendo unas características muy parecidas a éstos.
- Es el producto adecuado para instalarlo en escaparates, oficinas, salas de representaciones o también para cubrir cuadros. Por otro lado, el vidrio antirreflectante puede añadir propiedades de aislamiento térmico y acústico si se combina con otras soluciones
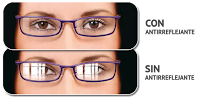
VIDRIO REFLECTANTE
- Se obtiene aplicando mediante pirólisis una capa metálica (silicio) sobre su superficie. Si no forma parte de un vidrio de cámara, la capa reflectante puede degradarse rápidamente. Además, consigue la máxima reflexión aunque disminuye mucho su transmisión lumínica
VIDRIO TINTADO
- Se obtiene a partir de añadir óxidos metálicos (hierro, cobalto o selenio) a la mezcla fundida del vidrio.
- Sus propiedades son: vidrios de diferentes colores según él metal utilizado: El verde se obtiene a partir de óxido de hierro. El gris se obtiene a partir de óxido de níquel. El bronce se obtiene a partir de selenio.
- Debido al incremento de la temperatura que alcanzan por absorción deben ser templados para garantizar su estabilidad.
El vidrio, debido a que es mal conductor del calor, si se expone a gradientes importantes de temperatura puede desarrollar tensiones internas que pueden provocar la fractura: Si una parte de un cristal se dilata y otra adyacente no lo hace, la primera trata de arrastrar a la segunda, ensanchándola, y por tanto generándole tensiones internas de tracción. Estas son las que pueden provocar una rotura.
Estrés térmico
Es un fenómeno que va ligado a la dilatación cuando el sol no incide por igual a la superficie de una lámina de vidrio. Todo vidrio que está expuesto al sol absorbe calor elevando así su temperatura y dilatándose, mientras que las zonas en obra permanecen sin dilatar. Estas dilataciones diferenciales pueden producir la rotura del vidrio.
VIDRIO INDUTRIAL
- No se utiliza como envase para productos alimentarios y otros, si no que se usa para ventanas de edificios, muros cortina, espejos, elementos vidriados en decoración, vehículos, etc.
VIDRIO DOMÉSTICO
- Se utiliza para almacenar productos alimentarios y de otros tipos de contenedores destinados a este fin.
- El reciclaje del vidrio comporta beneficios ambientales:
- Disminución del volumen de residuos municipales.
- Disminución de la contaminación atmosférica en un 20% y de las aguas en un 50%.
- Ahorro de recursos naturales. El vidrio es 100% reciclable y mantiene el 100% de sus cualidades después de un nuevo proceso de fusión enfriamiento.
El proceso de fabricación del vidrio ha ido evolucionando gracias a las mejoras tecnológicas, así encontramos métodos desde el tradicional vidrio soplado (s.XX) hasta el vidrio flotado.
Vidrio soplado:
- Encarada a la producción de objetos de uso cotidiano, especialmente aceiteras, porrones, potes, lámparas y garrafas. La fábrica cuenta con un horno con múltiples bocas ante las que están los morteros, unos dedicados a la fusión del material y otros al trabajo. En el mortero se pone el material llamado "casco" formado por vidrio aplastado, sílice, sosa y algún otro elemento (manganeso, cobalto...) en función de la vasija que se quiere producir y se calienta en el horno a altas temperaturas, alrededor de los 1300 º C. Allí al fundirse se forma la pasta que posteriormente se trabaja. La mayoría del vidrio producido tiene como materia prima el vidrio reciclado; cuando llega al horno es necesario seleccionarlo, sacar las partes inservibles, como etiquetas, tapones... Proceso de redondo a plano:
- Encarada a la producción de objetos de uso cotidiano, especialmente aceiteras, porrones, potes, lámparas y garrafas. La fábrica cuenta con un horno con múltiples bocas ante las que están los morteros, unos dedicados a la fusión del material y otros al trabajo. En el mortero se pone el material llamado "casco" formado por vidrio aplastado, sílice, sosa y algún otro elemento (manganeso, cobalto...) en función de la vasija que se quiere producir y se calienta en el horno a altas temperaturas, alrededor de los 1300 º C. Allí al fundirse se forma la pasta que posteriormente se trabaja. La mayoría del vidrio producido tiene como materia prima el vidrio reciclado; cuando llega al horno es necesario seleccionarlo, sacar las partes inservibles, como etiquetas, tapones... Proceso de redondo a plano:
1. Soplando una puesta hacia abajo con lo que se formaba un cilindro de gran longitud y diámetro. Al estar frío, se cortaba el mismo por sus extremos y se abría el cilindro por una generatriz, después se volvía a calentar y se allanaba sobre una mesa.
2. Haciendo girar la caña rápidamente sin soplar en posición horizontal y manteniendo el vidrio caliente por sucesivas introducciones en la mufla, la fuerza centrífuga hacía que el vidrio formase una especie de disco muy aplanado.
2. Haciendo girar la caña rápidamente sin soplar en posición horizontal y manteniendo el vidrio caliente por sucesivas introducciones en la mufla, la fuerza centrífuga hacía que el vidrio formase una especie de disco muy aplanado.
VÍDEOS DEL VIDREO SOPLADO
https://www.youtube.com/watch?v=PItHoRxTZyk
https://www.youtube.com/watch?v=Ax_wJyHImHU
Vidrio flotado
Tradicionalmente llamado vidrio plano es el único que se utiliza actualmente por los arquitectos y diseñadores en sus construcciones. Su proceso de fabricación consiste en hacer pasar el vidrio fundido por encima de una piscina de estaño a 1000 º C de manera que la masa de vidrio flote y se extienda horizontalmente sobre él. Al estar a altas temperaturas, este vidrio que se va fundiendo, va eliminando sus irregularidades hasta volverse plano, paralelo a la capa de estaño. Posteriormente, esta lámina se enfría lentamente y va avanzando sobre unos rodillos (sin que estos afecten su cara inferior) hasta pasar por una cámara de recocido y entonces sólo falta cortarlo. Este vidrio es insustituible cuando se quiere obtener una visión clara, sin distorsión óptica, y es la materia prima por excelencia para ser transformado en vidrio templado, laminado, fabricar espejos y unidades de doble acristalamiento hermético.